
How to improve the production capacity of cone crusher? Dry goods to share!
Time:2023-07-12 Back to list
If you are looking for related products or have any other questions, please feel free to call our sales hotline or click the right button to ask for a quote online!
Cone crusher is a secondary crushing equipment commonly used in sand and gravel production, which can crush stones with medium hardness and above. The crusher has high production capacity, wear resistance, good gradation of output stones, and round grain shape. It is popular among users. Most manufacturers only pay attention to its own * parameters when purchasing equipment, and ignore how to operate it after it is put into production. Increase its production capacity to a certain extent, resulting in less output of finished stones and low income. Next, the editor will share with you the method of increasing the production capacity of the cone crusher.

1. The parameters of the discharge port remain unchanged
According to the particle size requirements of the finished product, the parameters of the discharge port are generally set in advance. To ensure the output and quality of the stones, the parameters of the discharge port of the cone crusher should remain unchanged. Otherwise, the particle size of the product will increase and the output of qualified stones will decrease. , which in turn affects the crushing * of the cone. It is recommended to check the parameters of the discharge port every time a shift is changed.
2. Try to keep running at full capacity
Cone crusher feeding should fill the crushing cavity as much as possible, and make full use of the production capacity within the upper limit of operation. The cone crusher operating with half cavity will not only reduce the production capacity, but also affect the product in terms of gradation, needle flakes, etc., resulting in the quality of the output stones. Difference.

3. Reasonably set the power and speed of the cone crusher
According to the working principle of the cone crusher, its actual power should not be lower than 40% of the rated power. In order to obtain proper "load bearing positioning" and maximize the utilization of production capacity, the actual power of the cone crusher should be set between 75% and 95% of the rated power. The speed of the central shaft of the cone crusher determines its production capacity. Setting a reasonable speed within the upper limit can increase the crushing efficiency and increase the production capacity. It is recommended to monitor the speed in real time. Once it drops, adjust it in time to prevent the material throughput from decreasing, the production capacity from decreasing, and the power consumption from increasing. .
4. The falling point of the feed port is aligned with the middle position of the feed port of the cone crusher
It is recommended to be equipped with a vertical deflector to place the feed point in the middle of the cone crusher feed port, so that the materials in the crushing chamber can be evenly distributed, ensuring a smooth crushing process and full utilization of production capacity.
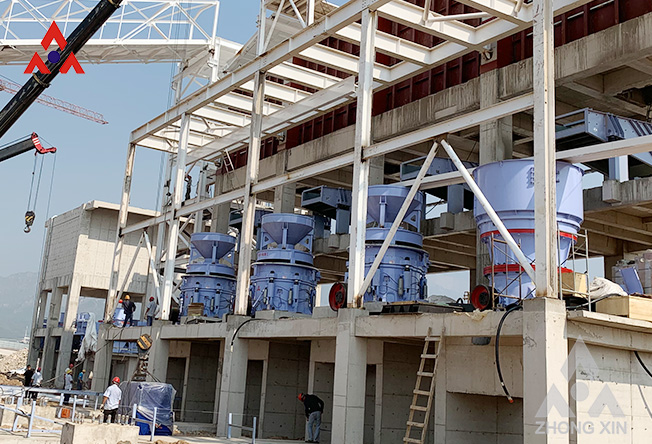
5. Ensure uniform feeding and control fine material content
When feeding, it is advisable to mix crushed stones of different particle sizes evenly. If the feeding is uneven, the side where the small-sized stones are concentrated will have a high density, which is easy to compact and block the material, which will affect the cone failure *. According to experience, for the second-stage cone crusher, the fine material content should not be higher than 25%, and the fine material can be filtered out by the vibrating screen, and the vibrating screen with suitable sieve hole diameter and screening capacity should be selected.

1. The parameters of the discharge port remain unchanged
According to the particle size requirements of the finished product, the parameters of the discharge port are generally set in advance. To ensure the output and quality of the stones, the parameters of the discharge port of the cone crusher should remain unchanged. Otherwise, the particle size of the product will increase and the output of qualified stones will decrease. , which in turn affects the crushing * of the cone. It is recommended to check the parameters of the discharge port every time a shift is changed.
2. Try to keep running at full capacity
Cone crusher feeding should fill the crushing cavity as much as possible, and make full use of the production capacity within the upper limit of operation. The cone crusher operating with half cavity will not only reduce the production capacity, but also affect the product in terms of gradation, needle flakes, etc., resulting in the quality of the output stones. Difference.

3. Reasonably set the power and speed of the cone crusher
According to the working principle of the cone crusher, its actual power should not be lower than 40% of the rated power. In order to obtain proper "load bearing positioning" and maximize the utilization of production capacity, the actual power of the cone crusher should be set between 75% and 95% of the rated power. The speed of the central shaft of the cone crusher determines its production capacity. Setting a reasonable speed within the upper limit can increase the crushing efficiency and increase the production capacity. It is recommended to monitor the speed in real time. Once it drops, adjust it in time to prevent the material throughput from decreasing, the production capacity from decreasing, and the power consumption from increasing. .
4. The falling point of the feed port is aligned with the middle position of the feed port of the cone crusher
It is recommended to be equipped with a vertical deflector to place the feed point in the middle of the cone crusher feed port, so that the materials in the crushing chamber can be evenly distributed, ensuring a smooth crushing process and full utilization of production capacity.
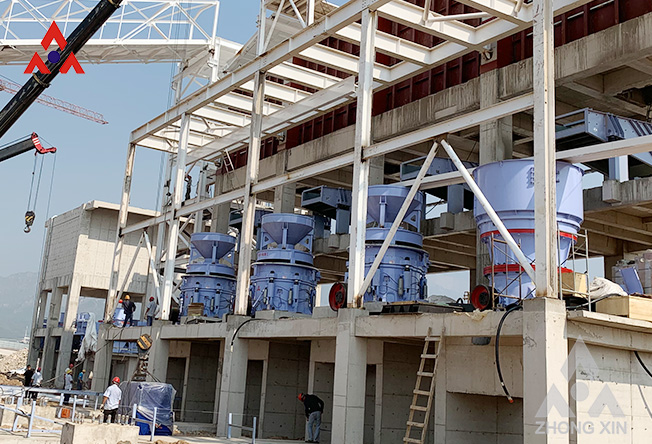
5. Ensure uniform feeding and control fine material content
When feeding, it is advisable to mix crushed stones of different particle sizes evenly. If the feeding is uneven, the side where the small-sized stones are concentrated will have a high density, which is easy to compact and block the material, which will affect the cone failure *. According to experience, for the second-stage cone crusher, the fine material content should not be higher than 25%, and the fine material can be filtered out by the vibrating screen, and the vibrating screen with suitable sieve hole diameter and screening capacity should be selected.
Leave message
Product Center
- Cone Crusher Machine
- • PXH series gyratory crusher
- • Single cylinder cone crusher
- • Spring Cone Crusher
- • Compound Cone Crusher
- • PSG Series Compound Cone Crusher
- Stone Crushing Machine
- • Sand Making Machine
- • Jaw Crusher
- • Vertical Shaft Impact Crusher
- • Impact Crusher
- Screening Sand Washing
- • XS Sand washing machine
- • circular Vibrating Screen
- • ZSW Series Vibrating Feeder
Materials
- • River Stone Crushing Processing
- • Iron Ore Crushing Processing
- • Aggregate Crushing Processing
- • Granite Crushing Processing
- • Basalt Crushing Processing
- • Gold Ore Crushing Processing
Contact Us
Add:Room 609,Easttower,xiyuan international square,Jianshe Road,Zhengzhou City,Henan Province,China
Tel:+86-371-67660555
Whatsapp:+0086-13676922906
Email:sales@zxcrusher.com
Web:www.zxstonecrusher.com